Ο απόλυτος οδηγός για υγρό καουτσούκ σιλικόνης (LSR) Injection Molding Κατασκευαστές
Υγρό καουτσούκ σιλικόνης (LSR) Χύτευση με έγχυση is a highly efficient and effective manufacturing process for producing high-quality, ακριβής, και ανθεκτικά προϊόντα. Αυτός ο οδηγός παρέχει μια λεπτομερή επισκόπηση της διαδικασίας χύτευσης με έγχυση LSR, τα πλεονεκτήματά του, εφαρμογές, προκλήσεις, και βασικές εκτιμήσεις κατά την επιλογή ενός προμηθευτή χύτευσης με έγχυση LSR.
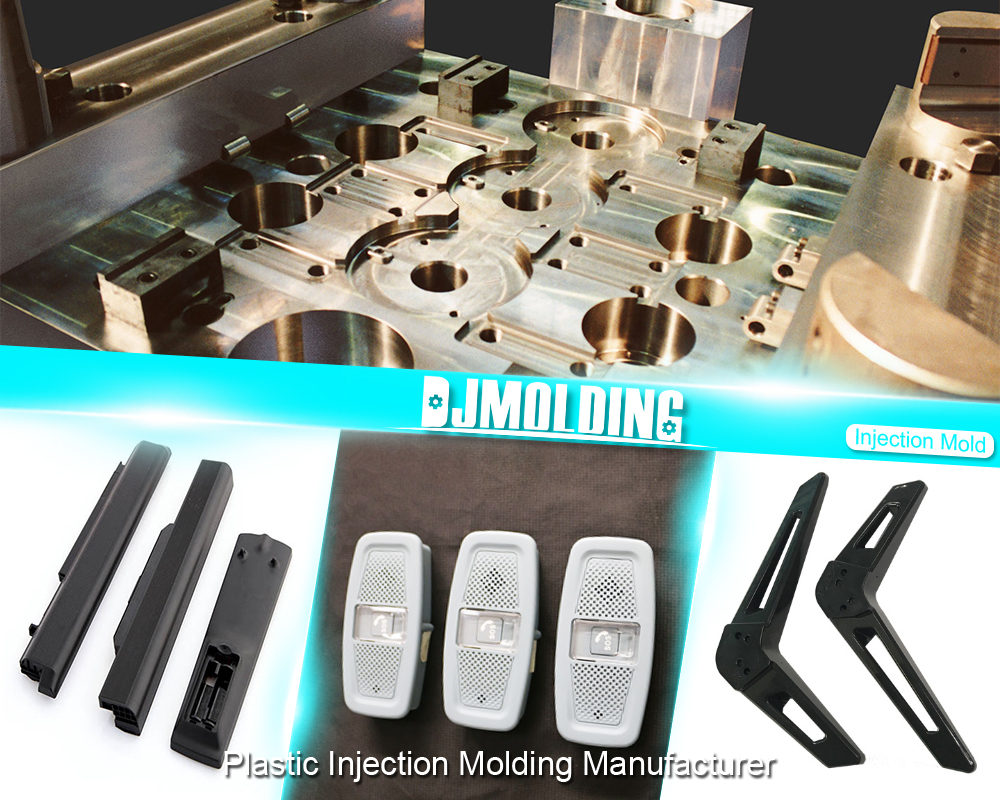
Εισαγωγή
Οι διαδικασίες παραγωγής έχουν προχωρήσει πολύ τα τελευταία χρόνια, with advancements in technology enabling the creation of high-quality, ακριβής, και ανθεκτικά προϊόντα. One such process that has gained popularity is Liquid Silicone Rubber (LSR) Χύτευση με έγχυση. This process involves injecting liquid silicone rubber into a mold and then curing it to form the desired product. LSR injection molding offers many advantages over traditional injection molding, including superior quality and precision, enhanced design capabilities, και οικονομική αποδοτικότητα. This guide will provide a comprehensive overview of LSR injection molding, τα πλεονεκτήματά του, εφαρμογές, προκλήσεις, και βασικές εκτιμήσεις κατά την επιλογή ενός προμηθευτή χύτευσης με έγχυση LSR.
What is LSR Injection Molding?
- Definition of LSR Injection Molding: LSR injection molding is a process used to produce parts made of liquid silicone rubber. It involves injecting liquid silicone rubber into a mold and curing it to form the desired product.
- How LSR Injection Molding Works: LSR injection molding works by injecting liquid silicone rubber into a mold. The silicone rubber is then cured by a heat source, such as a hot runner or an oven, to form the desired product. The designers include the product with the desired shape, texture, and dimensions in the mold design. LSR injection molding is an exact process for creating complex geometries and intricate designs.
- Comparison to Traditional Injection Molding: Traditional injection molding involves injecting molten plastic into a mold and then cooling it to form the desired product. LSR injection molding differs from traditional injection molding, using liquid silicone rubber instead of plastic. LSR injection molding offers several advantages over conventional injection molding, including greater precision, better quality, and the ability to produce complex geometries.
Advantages of LSR Injection Molding
LSR injection molding offers numerous benefits over traditional injection molding, making it an attractive manufacturing process for many industries. Here are some of the advantages of LSR injection molding:
Superior Quality and Precision
LSR injection molding offers exceptional precision and accuracy when producing complex, intricate parts. Due to its low viscosity, the LSR material can flow into rigid molds with high accuracy and detail, creating pieces with consistent dimensions and quality. Επιπροσθέτως, the LSR material does not shrink or warp during curing, διασφαλίζοντας ότι το τελικό προϊόν πληροί τις απαιτούμενες προδιαγραφές.
Wide Range of Durometers
LSR injection molding offers a wide range of durometers, which are measures of a material’s hardness or softness. They can tailor LSR to specific specifications and needs based on the intended use. Για παράδειγμα, they can formulate LSR as soft and flexible for medical devices or stiff and rigid for automotive parts.
High Chemical and Temperature Resistance
LSR materials resist high temperatures and harsh chemicals, making them suitable for demanding environments.LSR is an excellent choice for automotive, αεροδιαστημική, and medical applications, as it can withstand high temperatures, exposure to chemicals, and sterilization.
Enhanced Design Capabilities
LSR injection molding offers enhanced design capabilities, including producing complex geometries, over-molding, and insert molding. Overmolding involves molding one material over another, while insert molding involves placing an insert or component inside the mold before the injection process. This feature enables the creation of parts using multiple materials or components, reducing the need for assembly and enhancing the final product’s performance.
Αποδοτική
While LSR injection molding may have higher upfront costs than traditional injection molding, it is cost-effective in the long run due to its superior quality, ακρίβεια, and durability. LSR parts have a longer lifespan and require less maintenance, resulting in lower overall costs.
Εφαρμογές LSR Injection Molding
LSR Injection Molding has a wide range of applications across various industries due to its superior quality, ακρίβεια, and durability. Here are some of the industries that commonly use LSR injection molding:
- Medical Devices and Equipment: LSR Injection Molding is widely used in the medical industry to manufacture various devices and equipment, such as catheters, pacemaker components, χειρουργικά εργαλεία, and hearing aids. LSR is an ideal material for medical applications due to its biocompatibility, resistance to bacteria and other pathogens, and ability to withstand sterilization processes. Επιπροσθέτως, LSR’s soft and flexible nature allows for the production of comfortable and ergonomic medical products that are easy to use.
- Εξαρτήματα αυτοκινήτων: The automotive industry often uses LSR Injection Molding to produce parts such as seals, παρεμβύσματα, συνδετήρες, and vibration dampers. LSR’s high-temperature resistance, αντοχή, and ability to withstand harsh environments make it ideal for automotive applications. LSR’s flexibility and low compression set make it a perfect material for sealing and gasket applications.
- Consumer Goods and Electronics: Manufacturers commonly use LSR Injection Molding to produce consumer goods and electronics, including smartphone cases, earbuds, and smartwatch bands. LSR’s flexibility and durability make it an ideal material for products that require a high degree of flexibility and can withstand repeated use. LSR is also resistant to UV radiation and can maintain its color and appearance over time.
- Aerospace and Defense: LSR Injection Molding is also used in the aerospace and defense industries to produce various components such as seals, παρεμβύσματα, and vibration dampers. LSR’s ability to withstand extreme temperatures, πίεση, and harsh environments makes it an ideal material for aerospace and defense applications.
Challenges of LSR Injection Molding
While achieving the desired outcomes, they must overcome several challenges presented by LSR Injection Molding despite its many advantages. Here are some of the key challenges of LSR Injection Molding:
Επιλογή Υλικού
Selecting the suitable LSR material is crucial for achieving the desired properties and characteristics of the final product. Many LSR materials are available, each with unique properties and features. Επομένως, it is essential to work with an LSR injection molding supplier who can provide the necessary expertise and guidance in selecting the suitable material for your specific application.
Tooling and Equipment
LSR Injection Molding requires specialized tooling and equipment to achieve the desired results. The tooling and equipment must be designed and manufactured to precise specifications to ensure the quality and consistency of the final product. Επιπροσθέτως, LSR Injection Molding requires precision control of temperature, πίεση, and other processing conditions, which requires specialized equipment and expertise.
Processing Conditions
LSR Injection Molding requires precise control of temperature, πίεση, and other processing conditions to achieve the desired properties and characteristics of the final product. Variations in processing conditions can result in defects or inconsistencies in the final product. Επομένως, it is vital to work with an LSR προμηθευτής χύτευσης με έγχυση who can provide the necessary expertise and equipment to ensure precise control of processing conditions.
Regulatory Compliance
Industries subject to regulatory compliance requirements, such as the medical and aerospace industries, use LSR Injection Molding extensively. Επομένως, it is essential to work with an LSR injection molding supplier who can provide the necessary expertise and support to ensure compliance with regulatory requirements.
Key Considerations When Choosing an LSR Injection Molding Supplier
When selecting an LSR injection molding supplier, businesses should carefully evaluate their options based on several factors. Here are some key considerations to keep in mind:
Experience and Expertise
One of the most critical factors when selecting an LSR injection molding supplier is their experience and expertise in this field. It is essential to choose a supplier with a proven track record of success in producing LSR parts that meet your industry’s specific requirements and quality standards. Experienced LSR injection molders can also provide valuable insights and recommendations on material selection, βελτιστοποίηση σχεδιασμού, and processing conditions, which can help reduce costs, βελτίωση της ποιότητας του προϊόντος, and shorten lead times.
Quality Management Systems
LSR injection molding is a complex process that requires strict adherence to quality management systems and procedures to ensure consistent product quality and performance. Επομένως, it is crucial to choose a supplier with a robust quality management system, such as ISO 9001, ISO 13485, or IATF 16949. These certifications indicate that the supplier has implemented rigorous quality control measures, such as traceability, process validation, and statistical process control, to ensure their products meet the required quality standards and regulatory requirements.
Material Selection and Testing
LSR injection molding involves working with various liquid silicone rubber materials with different properties and characteristics. Επομένως, choosing a supplier with expertise in material selection and testing is crucial to ensure they select suitable material for your specific application. A reliable supplier should have access to a wide range of LSR materials and conduct thorough material testing, such as tensile testing, tear testing, and compression set testing, to ensure that the material meets the required specifications and performance requirements.
Design and Engineering Capabilities
LSR injection molding allows for greater design flexibility and freedom than traditional injection molding but requires specialized design and engineering expertise. Επομένως, choosing a supplier with solid structure and engineering capabilities is essential and can help optimize your product design for LSR injection molding. We can assist you with various aspects of the manufacturing process, such as designing parts, καλούπια, and prototypes. We can also provide feedback and recommendations to ensure easy manufacturing of the final product.
Manufacturing Capacity and Flexibility
Τελικά, when selecting an LSR injection molding supplier, it is essential to consider their manufacturing capacity and flexibility. As part of the evaluation process, we believe in their equipment, production capabilities, and ability to handle various production volumes and lead times. A reliable supplier should have sufficient manufacturing capacity to meet your production needs and the flexibility to adjust production schedules and books based on changing demand or project requirements.
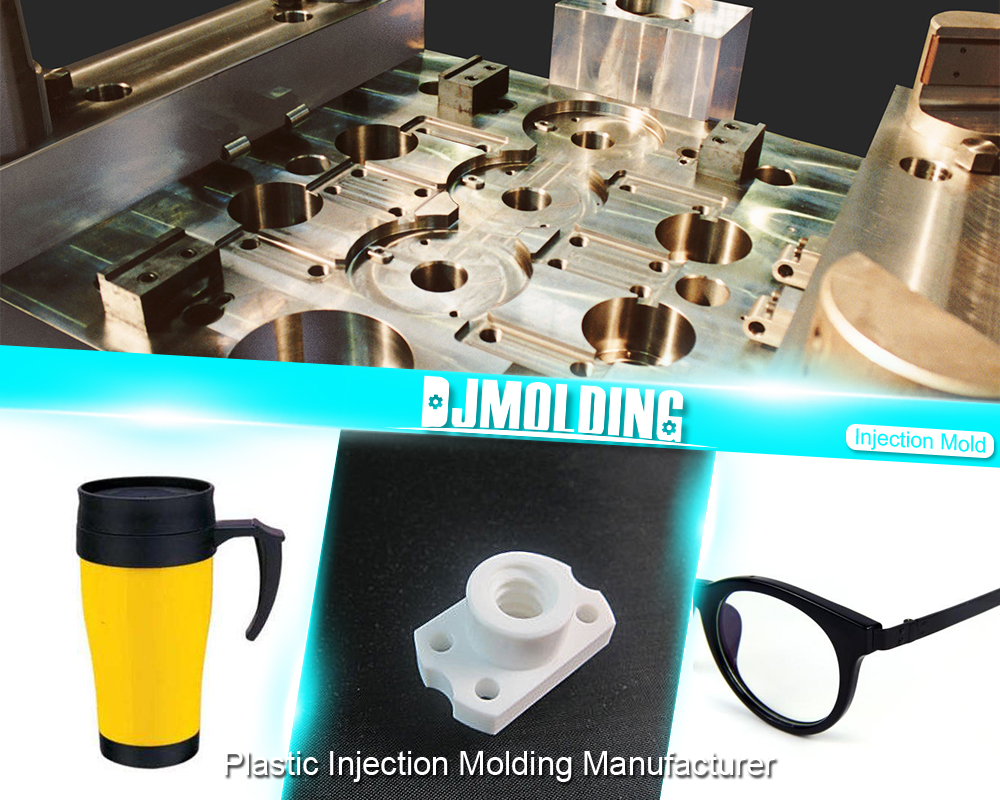
ΣΥΜΠΕΡΑΣΜΑ
Υγρό καουτσούκ σιλικόνης (LSR) Χύτευση με έγχυση is a highly versatile and efficient manufacturing process for producing high-quality, ακριβής, και ανθεκτικά προϊόντα. It offers a range of advantages over traditional injection molding, including superior quality and precision, enhanced design capabilities, και οικονομική αποδοτικότητα. LSR injection molding has many applications in various industries, including medical, αυτοκινητοβιομηχανία, καταναλωτικά αγαθά, αεροδιαστημική, and defense. Ωστόσο, it also presents several challenges, such as material selection, εργαλεία, and processing conditions. Επομένως, choosing a reliable and experienced LSR injection molding supplier who can provide the necessary expertise, quality management systems, and manufacturing capabilities is crucial. By considering these key factors, businesses can ensure the success of their LSR injection molding projects and achieve their desired outcomes.
For more about the ultimate guide to υγρό καουτσούκ σιλικόνης (lsr) κατασκευαστές χύτευσης με έγχυση,μπορείτε να κάνετε μια επίσκεψη στο Djmolding στο https://www.djmolding.com/liquid-silicone-rubberlsr-injection-molding/ για περισσότερες πληροφορίες.
Άρθρο Αρχικό Από: https://www.djmolding.com/the-ultimate-guide-to-liquid-silicone-rubber-lsr-injection-molding-manufacturers/