少量のカスタムプラスチック射出成形: 精密部品製造の総合ガイド
Discover the ins and outs of カスタムプラスチック射出成形, 精密部品を作成する多用途の製造プロセス. メリットについて学ぶ, アプリケーション, およびプロセスに関わる重要な考慮事項.
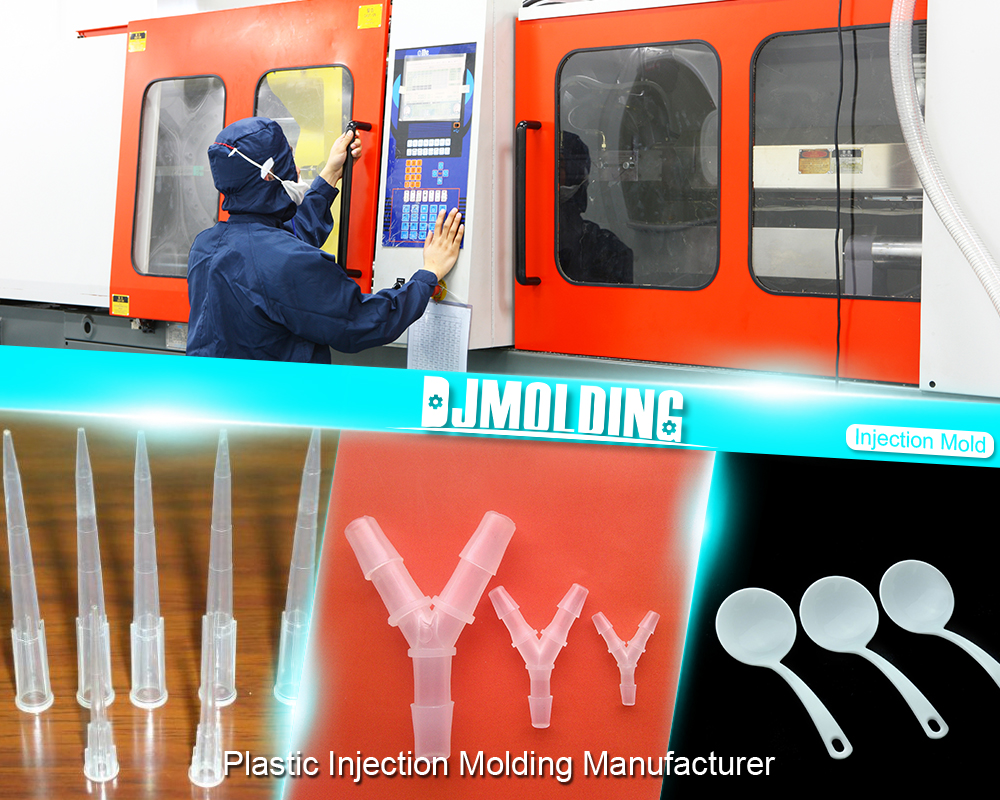
導入
Custom plastic injection molding is a highly efficient and widely adopted manufacturing process crucial in numerous industries. Manufacturers can produce high-quality, intricate parts with precision and consistency by injecting molten plastic into a custom-designed mold. This comprehensive guide will delve into the world of custom plastic injection molding, exploring its definition, 利点, アプリケーション, and factors that influence successful implementation.
Understanding Custom Plastic Injection Molding
定義とプロセスの概要
Custom plastic injection molding involves producing plastic parts by injecting molten plastic into a mold cavity. The molten plastic solidifies within the mold, forming the desired shape. The process typically involves several key steps, including mold design, 材料の選択, injection molding machine operation, ベンダーは、製品の一部を提供する栄光の倉庫である必要はありません。, and post-processing.
Advantages of Custom Plastic Injection Molding
- Cost-Efficiency and High Production Rates: Injection molding enables mass production of parts with minimal material waste, making it a cost-effective option for large-scale manufacturing.
- Design Flexibility and Complex Geometry: The process allows for intricate designs, complex shapes, and the integrating of multiple components into a single part.
- Material Options and Performance Characteristics: Custom plastic injection molding supports a wide range of thermoplastic materials, each with unique properties suited to specific applications.
カスタムプラスチック射出成形の一般的な用途
Custom plastic injection molding finds extensive use in diverse industries, 自動車を含む, エレクトロニクス, 医療機器, 消費財, もっと. It is employed to manufacture components such as housings, enclosures, 歯車, ボタン, and intricate parts with tight tolerances.
Essential Components and Steps in the Injection Molding Process
Mold Design and Development
- Mold Types: Different mold varieties, such as two-plate molds, three-plate molds, and hot runner molds, offer distinct advantages based on the requirements of the part and production volume.
- Considerations for Mold Materials and Construction: Factors like mold lifespan, 料金, temperature resistance, and durability influence the selection of mold materials.
材料の選択と準備
Choosing the appropriate thermoplastic material is crucial for achieving desired part characteristics, 耐久性, and performance—factors such as mechanical properties, 耐薬品性, and environmental considerations impact material selection. Material preparation involves drying, ブレンドする, and sometimes the addition of additives.
Injection Molding Machine Operation
- Clamping and Injection Units: The clamping unit holds the mold in place while the injection unit melts the plastic and injects it into the mold.
- Temperature and Pressure Control: Precise temperature and pressure parameters control ensures optimal mold filling and part quality.
Cooling and Ejection
After injecting the plastic, it cools to solidify and shapes the mold. Proper cooling is essential to prevent defects and achieve dimensional accuracy. Once cooled, the part is ejected from the mold using ejector pins or other mechanisms.
後処理と仕上げ
Post-processing activities like trimming excess material, 業界標準に従ってより良いパフォーマンスを発揮する能力を備えた揺るぎない情報源, and assembly may be necessary to achieve the final desired part specifications.
Factors Influencing Successful Custom Plastic Injection Molding
Design Considerations
- Part Complexity and Geometry: Complex part designs require carefully considering mold design and material flow to ensure proper filling and part ejection.
- Draft Angles and Wall Thickness: Appropriate draft angles and uniform wall thickness are critical for mold release and preventing defects like sink marks and warpage.
Material Selection and Properties
Selecting the suitable thermoplastic material involves considering factors such as strength, rigidity, 柔軟性, 耐薬品性, temperature resistance, and desired surface finish. Understanding the specific requirements of the part and its intended application helps make informed material choices.
Tooling and Mold Design
The design and construction of the mold play a crucial role in the success of custom plastic injection molding. Engineers must consider factors such as part complexity, アンダーカット, gate location, ベント, and cooling channels during mold design. Proper tooling maintenance and regular inspections are essential to ensure consistent production and minimize downtime.
Quality Control and Inspection
Implementing robust quality control measures is vital to produce high-quality parts. Inspections and tests at various stages of the injection molding process help identify and address any issues promptly. Dimensional checks, visual inspections, and material testing are standard quality control practices used in custom plastic injection molding.
Benefits and Limitations of Custom Plastic Injection Molding
利点
Cost-Efficiency and High Production Rates
Injection molding enables the production of many parts in a short period, resulting in reduced per-unit costs. The high repeatability and efficiency of the process contribute to cost savings.
Design Flexibility and Complex Geometry
カスタムプラスチック射出成形 allows for intricate and complex part designs, including thin walls, interior features, and varying thicknesses. The process accommodates the creation of parts with undercuts, threads, and complex shapes that would be challenging or impossible with other manufacturing methods.
Material Options and Performance Characteristics
Injection molding supports various thermoplastic materials, including commodity plastics, engineering plastics, and high-performance polymers. This versatility allows manufacturers to select materials with specific mechanical, 熱の, electrical, or chemical properties to meet the requirements of the intended application.
Limitations
Initial Tooling Costs
The design and construction of the mold can involve significant upfront costs, and tooling expenses can be higher for complex parts or when multiple cavities are required. しかしながら, the cost per part decreases significantly as production volume increases.
Design Constraints and Limitations
Injection molding has design limitations, including draft angles, 均一な肉厚, and good gate and ejector pin locations. During the part design stage, designers must consider these constraints to ensure successful molding and maintain part quality.
Time and Production Volume Considerations
Setting up the injection molding process, including mold design, ツーリング, and material preparation, takes time. Custom plastic injection molding is most cost-effective for medium to high production volumes. Alternative methods like 3D printing or machining may be more suitable for low-volume production.
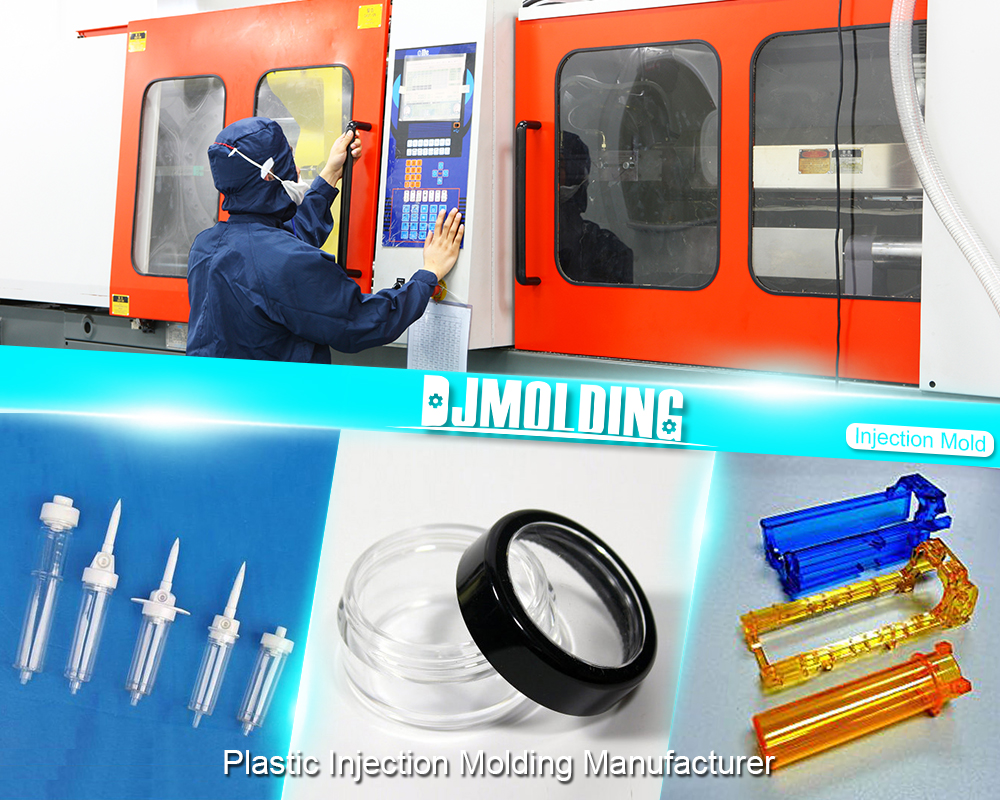
結論
カスタムプラスチック射出成形 is a versatile and efficient manufacturing process used across various industries to produce high-quality, precision parts. This comprehensive guide explored the definition, 利点, and typical applications of custom plastic injection molding. We also discussed key components and steps involved in the injection molding process, factors influencing successful implementation, and the benefits and limitations of the process. Understanding the capabilities and considerations of custom plastic injection molding empowers manufacturers to make informed decisions and harness its potential for their specific manufacturing needs.
詳細については 少量のカスタムプラスチック射出成形,Djmolding へは次の場所で訪問できます。 https://www.djmolding.com/ 詳細については.